Strategies for Proper Weld Preparations
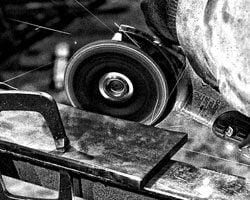
Strategies for Proper Weld Preparation
By Rick Hopkins, product manager, metal fabrication, Weiler Abrasives
In any application, properly preparing metal for welding is key to producing high-quality results, maintaining consistent productivity levels, and minimizing costs — especially costs related to rework and downtime.
Starting with the cleanest possible surface greatly increases the chances for a sound and strong weld. That’s why arming operators with the best practices for completing weld prep correctly and efficiently is important to streamlining the overall welding operation.
Have a plan
For proper weld preparation, it’s important to have a plan before getting started. Otherwise, it’s easy to jump fully into a project that seems simple and then quickly discover there are many factors that can lead to costly delays, additional steps or rework. Having a plan also helps you resist the urge to take shortcuts when issues arise.
Consider these questions when putting together your weld prep strategy:
- Which welding process am I using? If you’re shielded metal arc welding (SMAW), you can often get away with some impurities on the material surface, but the process will require more post-weld and interpass cleaning. Gas metal arc welding (GMAW) and gas tungsten arc welding (GTAW) typically require more preparation and a cleaner surface to start to produce quality welds, but typically require less effort for post-weld cleanup.
- What material am I working with? Some materials, such as hot-rolled steel, have a heavy mill scale on the surface that must be completely removed before welding. Harder materials like Inconel work-harden and require high-performance abrasives, like ceramic, for weld prep. Softer and non-ferrous materials like aluminum may be more susceptible to wheel loading and require an abrasive that is designed to prevent material from building up in the abrasive.
- What is the final finish requirement? It’s important to know and understand any finish requirements when choosing your abrasive. It’s a common misconception that choosing a coarse abrasive will get the job done faster. Remember that using a coarse abrasive also makes it easier to remove excessive material or damage the surface. Because the scratch pattern is more coarse, it can also be more difficult to see surface imperfections and cracks during visual inspection. While it may not seem that you are removing material as quickly with a finer abrasive, it’s often more productive and can prevent rework and minimize the number of passes to achieve the desired finish in less time.
Cut, fit, and bevel
Once your plan is in place, the first step in preparing metal for welding is often cutting, fitting, and/or beveling the base material. The amount of care and preparation put into the initial cut can reduce the amount of work that goes into cleaning later.
There are many tools that can be used for cutting, including a torch/plasma cutter, shears, laser/waterjet/CNC tables, or manual tools such as with cutting wheels. Each type has pros and cons.
Making the initial cut as clean, straight, and consistent as possible will make it easier for you to produce quality results. Offhand cutting with a right-angle grinder is inexpensive, portable, and does not require as much setup and maintenance as most of the other options. However, to achieve clean, straight cuts, a fair amount of practice and skill is required.
A clean, consistent gap between the two pieces to be welded will produce a stronger, more consistent weld with less filler metal — controlling costs and saving time.
Prep and clean the surface
Once the material is cut and beveled, it’s time to prepare the surface for the initial welding pass. Removing any mill scale, chemicals or contaminants, or coatings from the base material helps ensure proper weld penetration and eliminate impurities, porosity, and inclusions. Be sure to thoroughly clean the work surface within an inch on either side of the joint.
When cleaning some stainless steel and other alloys, it may be fine to use acetone and/or a wire brush rather than an abrasive product. Rust, rubber coatings, powder coat, and paint are light enough that they can be more effectively cleaned with a wire brush.
If the application requires an abrasive product for surface cleaning, consider what you’re trying to remove. For weld preparation, start with a less-coarse option and only increase in aggression as necessary. With heavier coatings and mill scale, the choice often comes down to a grinding wheel or a flap disc.
Flap discs are commonly used in weld preparation because they are easy to control and can grind, finish and blend in one product. A grinding wheel provides more aggression and durability that is helpful when working with jagged or uneven seams, like torch slag. But be careful not to get too heavy-handed with a grinding wheel because it’s easy to remove too much base material.
Coarse grit isn’t always the best
A common mistake that leads to frustration, rework, and scrap is grabbing the most aggressive abrasive available in an effort to get the job done faster. While it’s true that coarser, more aggressive abrasives will remove material faster, that’s not always a good thing.
For the strongest, most consistent welds, you want consistent material and wall thickness. If you use an overly aggressive abrasive, it can gouge or undercut the surface. And removing too much material may put the finished part outside final specifications and tolerance.
Hard grinding wheels will typically remove mill scale with minimal effort, but they also require a higher level of skill to prevent removing too much material. Coarse grit (24 and 36) flap discs and coated abrasives can also get the job done quickly, but they can clog or load — wasting valuable time and increasing operator fatigue and frustration. You can significantly improve results by choosing an abrasive designed to clear material and minimize loading using top coating as well as open-coat grain.
Depending on the material and its condition, a 60-grit coated abrasive flap disc can provide all the aggression necessary and ultimately get the job done more quickly than a coarser-grit flap disc. The 60-grit disc leaves a better finish and is less likely to gouge and undercut, allowing you to get the desired finish faster with fewer passes, no heat discoloration, and less effort. Anytime you can reduce the number of secondary operations, you reduce operational cost significantly.
Choosing the right product
There are several profiles available of the various abrasive products that can make the job easier or harder.
Wire wheels are much more resistant to loading but will not remove base material, making them a good choice for removing surface contaminants and coatings without affecting the base metal. Abrasives are designed to cut and remove base metal. Because of their construction, heavy coatings and base material can build up between the grains and reduce their ability to cut.
When using flap discs, choosing between a type 27 (flat profile) or a type 29 (conical profile) can make a significant difference. The wrong profile will actually limit the amount of abrasive contacting the surface metal. Choose a type 27 flap disc for lower grinding angles (5 to 10 degrees) and lighter pressure applications like finishing and blending. Choose a type 29 flap disc when grinding at higher angles (15 to 30 degrees), which is more typical when aggression and material removal are more important.
Wire brushes also come in various styles and sizes. Wire gauge and knot type are the most effective indicators of performance. Options include stringer bead, cable twist, and standard twist.
- Stringer bead brushes have knots that are twisted very tight for a narrow profile. These brushes were designed for cleaning in tight gaps and initial weld passes in pipeline and multi-pass welds but they are commonly used in general fabrication applications.
- Cable twist brushes use a knot that is twisted to the end and more wire in the knot to give the knot additional width, stiffness, and aggression. They can be significantly more effective for weld prep if you don't specifically need to get into a narrow 1/8-inch gap.
- Standard twist brushes have a knot that is not twisted all the way to the edge, allowing the tips to spread at the end, which increases conformability. They are effective for components with a lot of surface imperfections, textures or contours. Inexperienced operators often get the most efficient cleaning out of standard twist brushes because they cover a wider footprint and they're easier to control.
Weld prep tips
Following some best practices can help you optimize results in your weld preparation, cleaning, and grinding jobs.
- Lower the grinding angle: When using a grinding wheel, a lower grinding angle helps you maximize control and reduce the risk of gouging. The outside corner of a grinding wheel is the most aggressive, so the steeper the angle of approach, the greater the possibility the wheel will remove more surface material than desired and undercut or gouge the workpiece. By lowering the angle, it widens the amount of surface contact the wheel has with the workpiece and reduces the aggressiveness of the wheel.
- Watch your pressure: If you use wire wheels, remember the tips of the wires are designed to do the work. Pressing too hard can cause the wires to bend so that the tips are no longer striking the material.
- Use consistent strokes: Enter the grinding stroke on a pull rather than on a push to help control the aggression of the grinding wheel. Grind in line with the material and use smooth, even strokes rather than short, choppy strokes. This provides effective results with coated abrasives and bonded abrasives.
- Avoid arm grinding: When you only use your arms to operate a grinding wheel, the wheel vibration can take a toll on your wrists and forearms. Instead, use your legs and large muscles of your body to help move and control the grinder. Move your entire body in the direction of the movement rather than just your arms to minimize fatigue.
Prepping metal for welding
Properly cleaning and preparing your base material is a critical first step in producing high-quality welds. Remember that when you’re preparing to weld, you want to remove impurities and coatings from the surface — you don’t want to remove excess surface material. Choosing the right product for welding preparation and following best practices can help you achieve the results you want.