Pressure Vessel Case Study Tiger Ceramic Discs Last Longer, Change Offers Cost Savings
Item # 69864
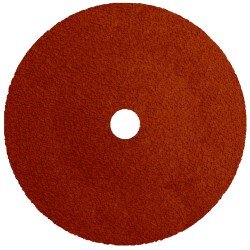
Challenge:
A leading supplier to the Petro Chemical industry was experiencing a high use of abrasives during the custom fabrication of pressure vessels, bulk storage tanks, and transport trailers. The welders were grinding torch cut edges with a ceramic resin fiber disc because they valued the combination of comfort and initial cut-rate RFD’s offered. However, they found that the discs would glaze over after a few minutes of use, and cut-rate would diminish. Welders discarded the discs when they noticed a loss of cut-rate. With over 30 welders working at multiple facilities, the company was looking to find an abrasive that would hold up to the demanding application and deliver longer life.
Solution:
Weiler Application Experts found the current discs used symmetric abrasives grains, which offered a high initial cut-rate but also a rapid reduction of performance.
Weiler Application Experts recommended Tiger Ceramic RFD’s because the grains fracture with less pressure, continuously exposing new sharp edges throughout the life of the disc while also preventing glazing. After testing, operators felt the new disc maintained a high cut-rate much longer.
Result:
The company found that Weiler’s Tiger Ceramic 24 grit RFD’s lasted more than 2.5 times longer before the operator required a new disc. Longer disc life in combination with a lower cost per disc resulted in an expected annual abrasives savings of $62,296.
2.5X Longer
$62,296/Year
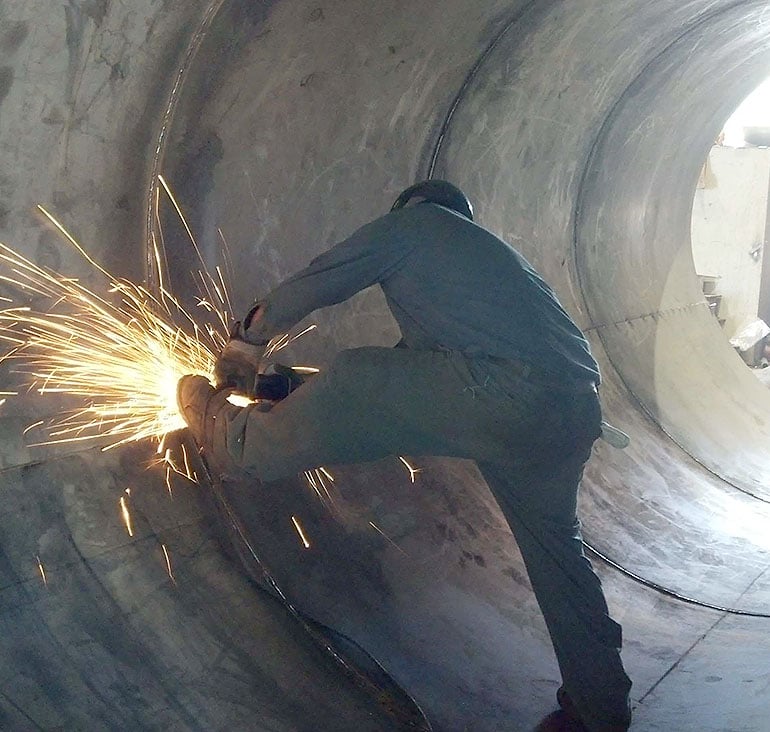
Schedule an On-Site Assessment
The first step to cutting through barriers is to schedule a free on-site assessment where Weiler experts will evaluate how our abrasives can help eliminate inefficiencies, safety issues, and labor shortages in your operation.
Our Approach To Improvement:
- On-Site Assessment
- Test Abrasives
- Measure Results
- Present Documented Cost & Time Savings
Related Resources
Schedule an On-Site Assessment
Don't let inefficiency, safety issues, or labor shortages hold your metal fabrication business back. Contact us today to learn more about how our abrasives for metal can help you achieve a smooth finish, prioritize safety, and address labor shortages with efficient and safe grinding solutions.