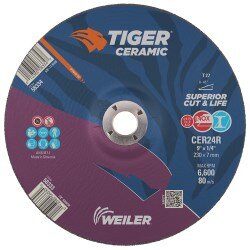
Challenge:
A leading heavy structural steel fabrication company located in Georgia, manufactures custom fabricated steel framing for building structures. Grinding wheels are used to grind welds and shape custom designs, so pieces fit up properly in the field. With competitor wheels, 75 fabricators used 100 9" wheels and 160 4.5" wheels each week. The company was looking for an abrasive that would increase productivity at a reduced cost.
Solution:
After testing several grinding wheels, the company found Tiger Ceramic removed metal 12% faster than the closest competitive wheel. Fabricators noted the edge of the wheel didn't round off as quickly as other wheels when grinding. The square edge maintained aggressive qualities of the wheel longer, getting the work done faster.
Result:
By converting to Tiger Ceramic grinding wheels, the company increased grinding productivity by 12% at a lower cost per wheel. The switch resulted in a savings of $18,987 annually on abrasives.
End User Comments:
”This Weiler disc holds it’s edge better than what I was using before. It’s aggressive too. It definitely grinds faster.” - Welder / Fabricator
12% Faster
$18,937/Year

Schedule an On-Site Assessment
The first step to cutting through barriers is to schedule a free on-site assessment where Weiler experts will evaluate how our abrasives can help eliminate inefficiencies, safety issues, and labor shortages in your operation.
Our Approach To Improvement:
- On-Site Assessment
- Test Abrasives
- Measure Results
- Present Documented Cost & Time Savings
Related Resources
Industrial consumables can be measured in life-cycle, safety, and productivity. Weiler Abrasives Consumable Productivity studies drive quantitative data, which can be measured and verified. Call Weiler's Customer Experience Team at 800.835.9999 or fill out the form below to learn how our industry experts can help you evaluate your consumable usage and help reduce it.
Schedule an On-Site Assessment
Don't let inefficiency, safety issues, or labor shortages hold your metal fabrication business back. Contact us today to learn more about how our abrasives for metal can help you achieve a smooth finish, prioritize safety, and address labor shortages with efficient and safe grinding solutions.