Cleaning and Grinding Multi-Pass Welds
Simply put, a multi-pass weld is when a butt weld requires more than one pass or layer. Multi-pass welds are necessary for many applications, including welds found in industries such as heavy-duty structural fabrication, pipeline, shipbuilding and repair, and pressure vessel fabrication. Adding layers of weld to thick metal joints increases critical weld strength where testing is often required, and weld failure could be catastrophic.
At Weiler, we understand that the wire brushes and abrasives play a critical role in the finished weld quality. That's why we are committed to developing products to help you get the job done right and done fast. And we don't stop there; we help you select the best product for your specific application.
Below are resources to help you learn more about our multi-pass welding products and solutions.
Download the Weiler Multi-Pass Welding Guide
Multi-Pass in 5 Steps
Any joint, whether tubing, plate, or structural, requires significant prep to ensure strong and consistent weld penetration. Setting the bevel is the first step, and 1/4” grinding discs are a popular choice. Flap discs, like Weiler’s Tiger Paw, are an excellent choice because they reduce vibration and increase control when beveling.
Weiler’s 1/8” pipeline wheel allows flat grinding, making it an excellent choice to quickly and effectively set the face (land).
Finally, the bevel must be cleaned. To achieve a proper union, it is important to remove any surface residue such as oil, rust, paint, primer, corrosion, burrs, or any impurity on the surface of the steel. Type 29 flap discs are aggressive, easy to control, and highly effective for cleaning, removing pits, and finishing the bevel. For cleaning a bevel that is torch cut use a Tiger aluminum back flap disc.
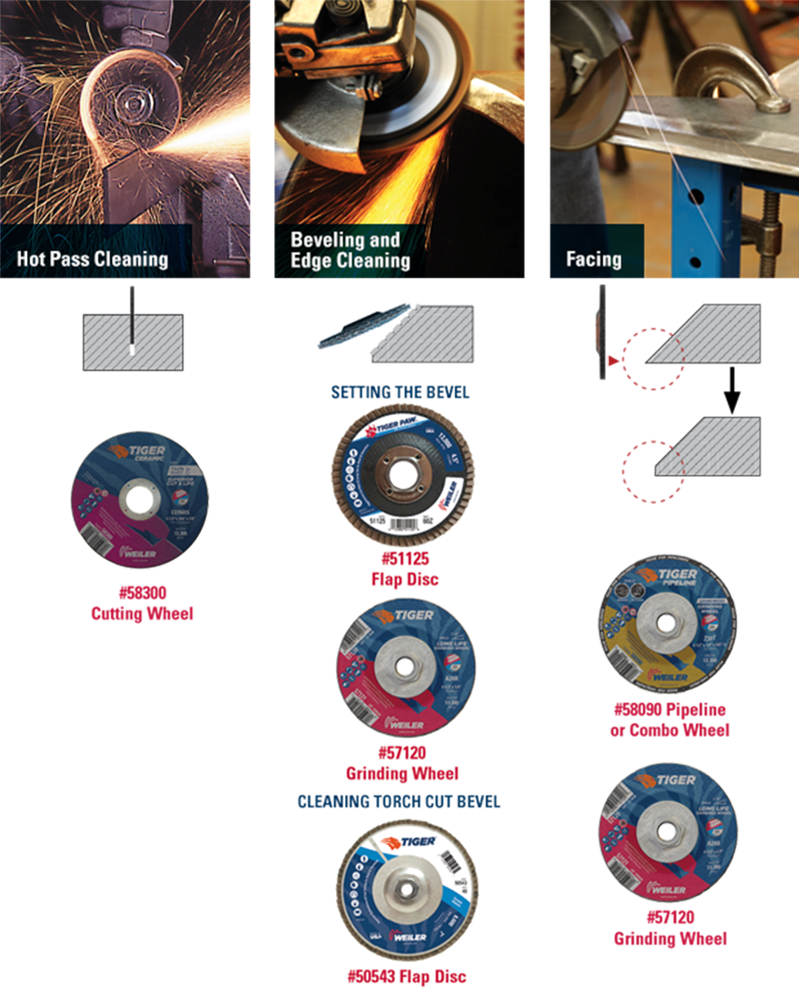
With the bevel and face cleaned and set, the joint is tack-welded to prepare for the root pass. The first weld bead applied to joints is called the stringer bead or root pass. The weld must penetrate 100%. Once the root pass is finished, a “U” shaped groove is ground using a notching or pipeline wheel. The objective is to prepare the base so that the next pass (hot pass) can fully penetrate the wall thickness to ensure a strong and solid joint.
The Pipeline wheel is ideal for grinding the root pass bead because it is designed to grind hot welds, biting into the bead and digging out the wagon tracks fast. Operators also commonly choose this wheel because it doesn’t glaze over or vibrate, providing a better overall grinding experience.
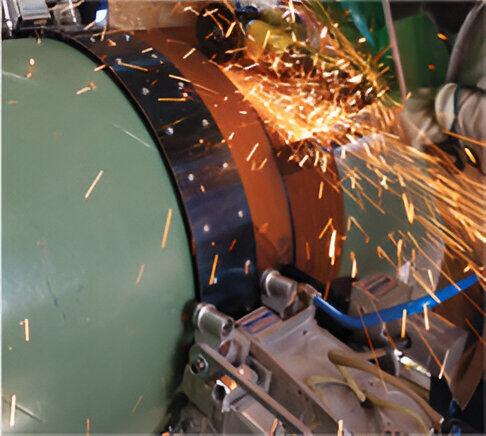
Mechanical Welding
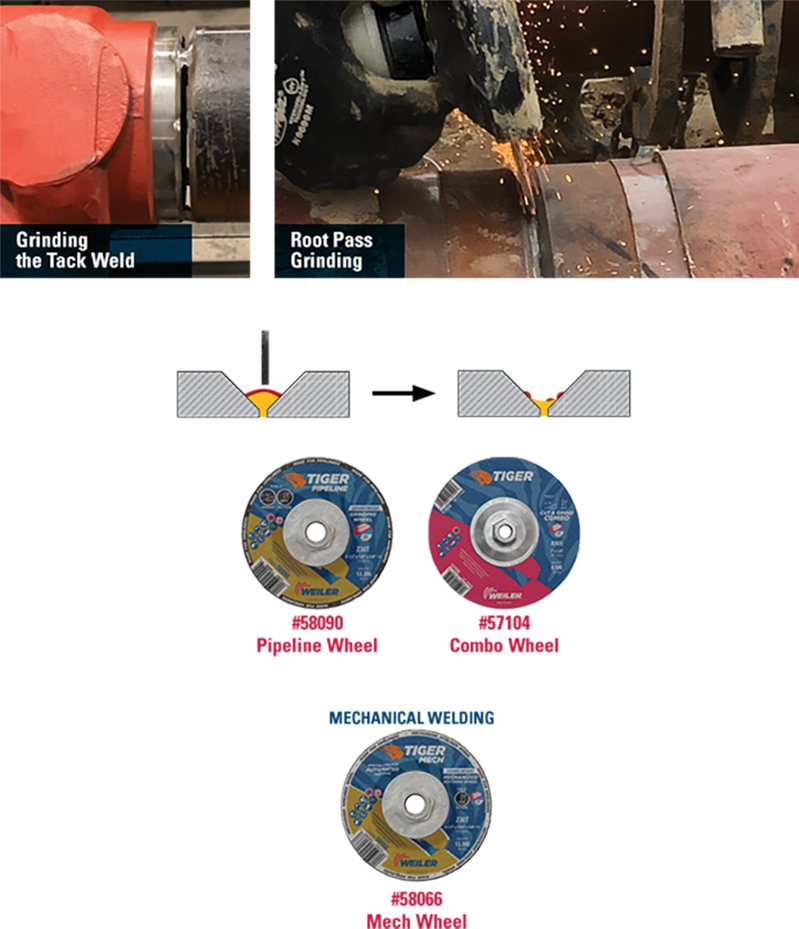
The next welding step is called the hot pass. To achieve maximum penetration of the weld at the ends, the hot pass should start as soon as possible to maintain a high temperature in the joint. When grinding after the root pass, slag residues are formed and exposed at the ends of the first bead. This hot pass is done ASAP to ensure that these residues are burned and flow out of the bead. That is why notching with a pipeline wheel and surface cleaning with a bead brush must be done quickly.
Stringer bead brushes and encapsulated brushes are excellent choices for cleaning the hot pass. Stringer bead brushes have narrow, tightly twisted knots for high-impact cleaning and aggression. The narrow profile (face) and aggressive cleaning make them popular for cleaning in narrow gaps between weld passes.
Encapsulated wheels feature a heat-stabilized encapsulation that gradually wears away to expose a consistent short trim for higher aggression, controlled brushing action, and longer life. Ideal for cleaning hot welds.
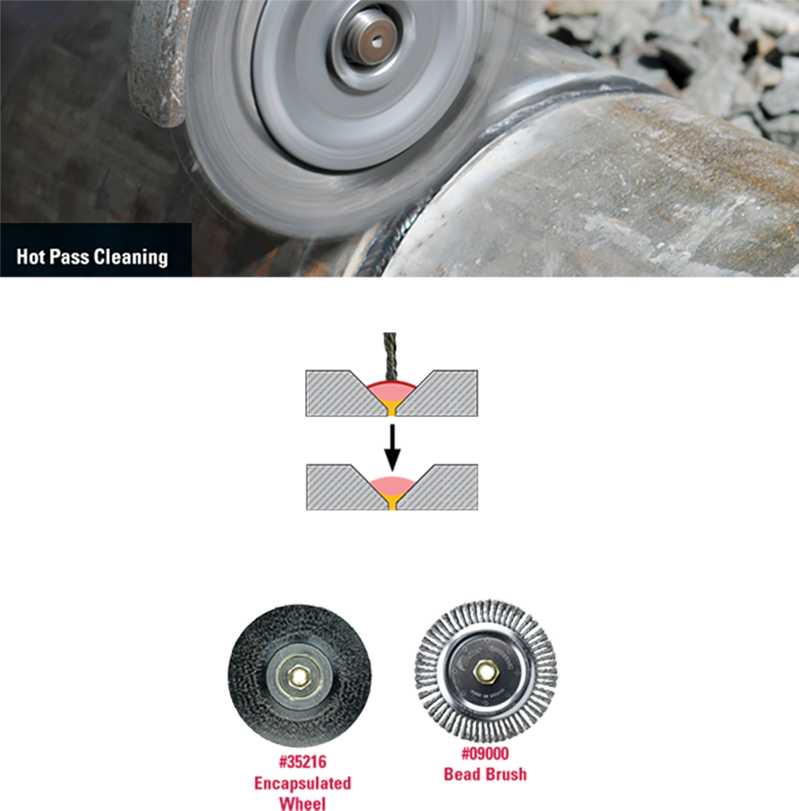
After cleaning the hot pass, the remaining gap must be filled with additional passes. The number of filler passes required will depend on the thickness of the wall and the width of the gap. To ensure optimal weld penetration, a perfectly clean surface is required prior to applying each bead. Root pass brushes or encapsulated brushes can be used to clean filler passes, however, a filler pass brush is a better choice for wider welds.
Filler Brushes have additional wire strands and a wider profile (face) for aggressive brushing and increased durability. Their wider contact area makes them an excellent choice for cleaning filler passes quickly and efficiently. They are also are often referred to as cable twist brushes.
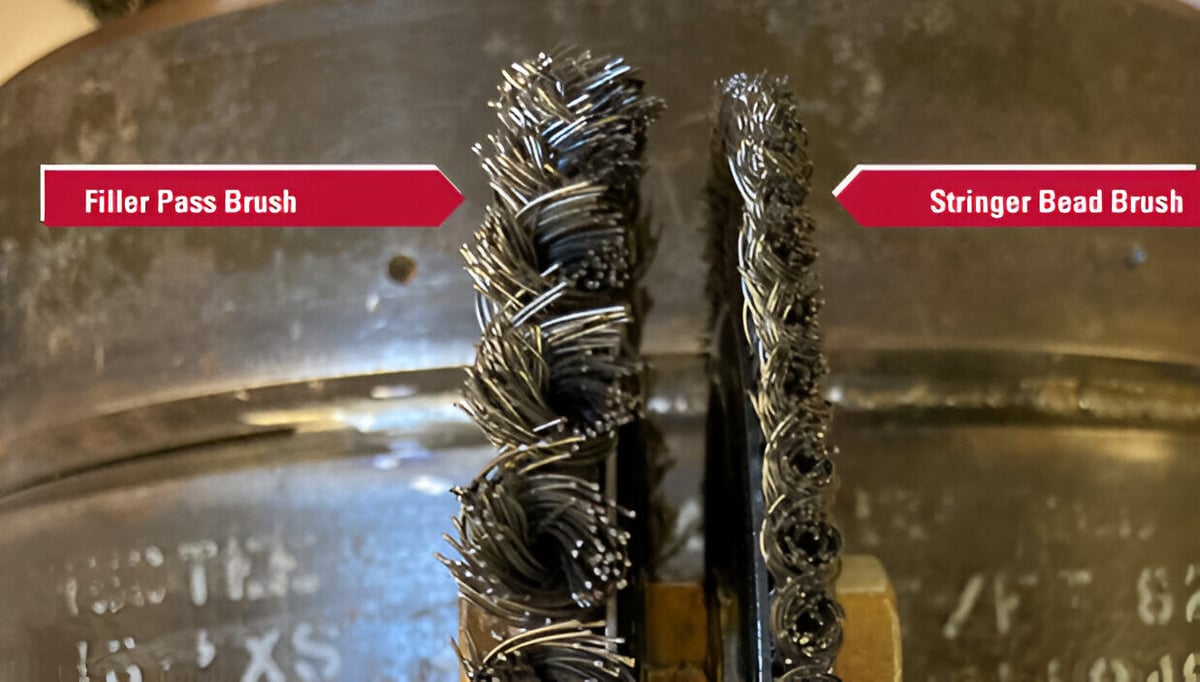
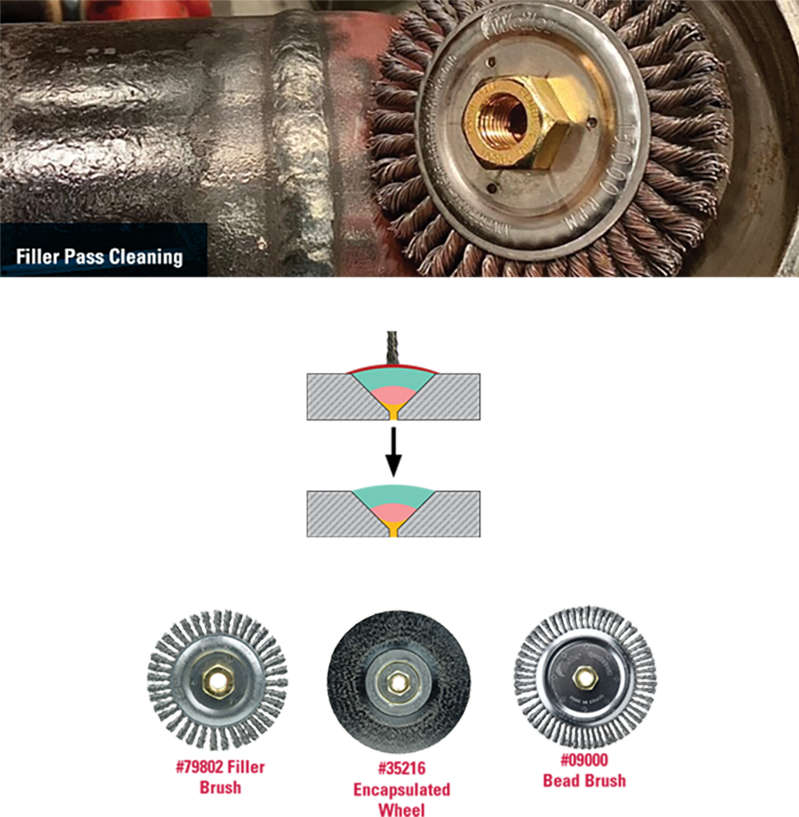
The capped pipe joint is typically coated with an epoxy or other protective coating. For this, Weiler recommends wood handle chip and oil brushes. Prior to applying any coating, the surface must be cleaned and prepped for optimal adhesion. Knot cup brushes provide fast, efficient cleaning and surface prep for wider surface areas. Knot wheels are also commonly used.
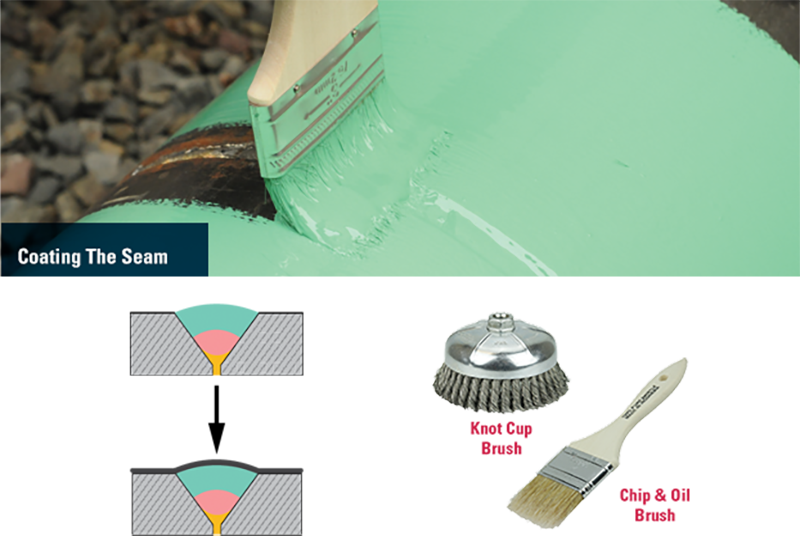
Productivity Programs
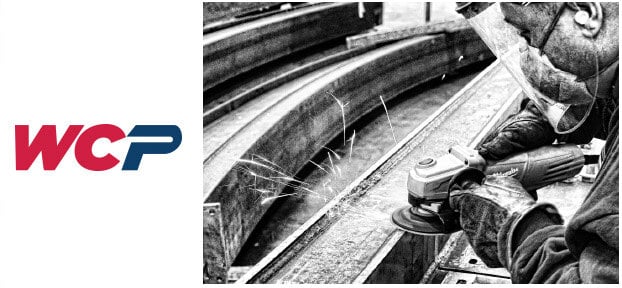
The Weiler Consumable Productivity (WCP) program utilizes a process to collect hard data around how abrasives are used, how long they last, and how productive they are. This process effectively compares several products and aids in selecting the best product for an application.
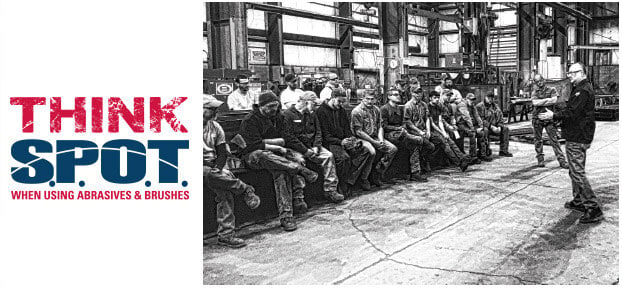
Weiler SPOT Safety Program helps end-users educate their workforce on the safe and proper usage of abrasives and the tools associated with them while supporting the compliance and usage of the correct PPE.