Shipyards: Overcoming Operational Challenges with High-Performance Abrasives Solutions
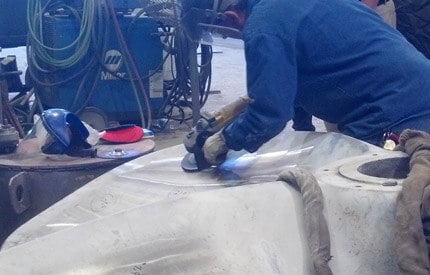
Recognizing Trends of the Shipbuilding and Ship-Repair Industry
Building a ship encompasses multifaceted operations like electrical installations, pipe fitting, structural welding, component assembly, etc. Precision and accuracy are imperative to pass inspection and limit costly rework.
Shipyards face numerous challenges that threaten to reduce their efficiency and slow down productivity. Shipbuilders face environmental challenges that lead to issues such as oxidation, rusting, and scaling. These need to be addressed throughout the welding and fabrication process. Welders & fitters are also challenged with working in confined spaces, often overhead, underscoring the importance of durable abrasive products to minimize downtime and enhance production.
Choosing the right abrasive for metal shipbuilding will:
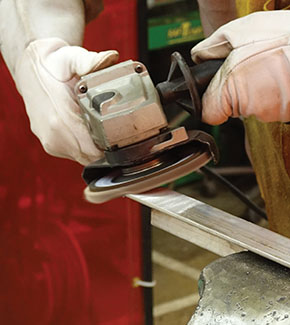
Improve the efficiency
Improve the efficiency
Choosing the right abrasive will allow for more efficient surface preparation, welding, and material removal.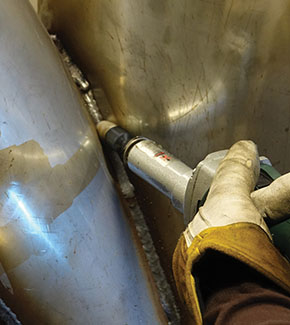
Weld Seam Cleaning & Finishing
Weld Seam Cleaning & Finishing
Welding is critical in shipbuilding and ship repair. Proper cleaning and preparation are necessary to ensure full penetration of welds.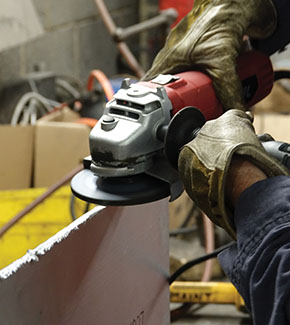
Minimize Cross-Contamination
Minimize Cross-Contamination
Utilizing specialized abrasives with a contaminant-free formula, and strict quality control and product segregation are essential to mitigate these issues.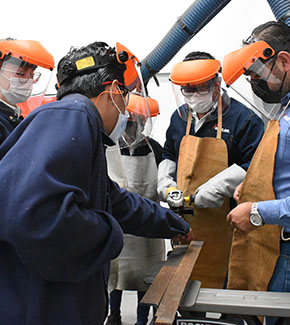
Increase Safety
Increase Safety
Training users on the safe and proper use of abrasives helps keep users safe, increases productivity and reduces lost work time and injury claims.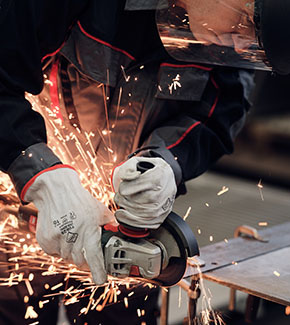
Offset Labor Shortages
Offset Labor Shortages
Providing users with the right abrasives can increase productivity and help offset labor shortages by increasing uptime and morale.Building a ship encompasses multifaceted operations like electrical installations, pipe fitting, structural welding, component assembly, etc. Precision and accuracy are imperative to pass inspection and limit costly rework.
Shipyards face numerous challenges that threaten to reduce their efficiency and slow down productivity. Shipbuilders face environmental challenges that lead to issues such as oxidation, rusting, and scaling. These need to be addressed throughout the welding and fabrication process. Welders & fitters are also challenged with working in confined spaces, often overhead, underscoring the importance of durable abrasive products to minimize downtime and enhance production.
The crucial areas where the shipbuilding and repair industry are met with operational challenges involve:
Efficiency and Productivity
Streamlining operational processes and reducing downtime are constant challenges in shipbuilding and repair. Choosing the right abrasive will allow for more efficient surface preporation, welding, and material removal.
Weld Seam Cleaning and Finishing
Welding is critical in shipbuilding and ship repair. Proper cleaning and preparation are necessary to ensure full penetration of welds.
Cross-Contamination
Shipbuilders face challenges when working with aluminum, stainless steel, and steel due to cross-contamination. This can affect weld quality, surface cleanliness, and aesthetic appearance. Utilizing specialized abrasives with a contaminant-free formula, and strict quality control and product segregation are essential to mitigate these issues.
Safety & Environmental Impact
In addition to operational challenges, shipyards must prioritize safety and environmental considerations. Training users on the safe and proper use of abrasives helps keep users safe, increases productivity and reduces lost work time and injury claims.

The SPOT Safety Program educates people on how to use abrasives and power brushes safely and properly. The program includes information regarding correct use, potential hazards, and safety tips.
Labor Shortages
For many shipyards, the biggest challenge is labor and not having enough people to do the work. Providing users with the right abrasives can increase productivity and help offset labor shortages by increasing uptime and morale.
Helping You Gain a Competitive Advantage
As an experienced global provider of abrasive solutions, Weiler Abrasives understands the unique needs of the shipbuilding and repair industry. We continuously innovate in response to emerging challenges to support the growth and sustainability of the shipbuilding and repair industry. Application experts work directly with shipbuilders at their facility to see production processes first-hand and work to resolve issues quickly. We help you choose the right abrasive for your applications to help you do more with less and increase efficiency, safety, and productivity.

Based on customers' data, the Weiler Consumable Productivity (WCP) program measures their total abrasives' operating costs and finds savings in operations that involve the use of abrasives.
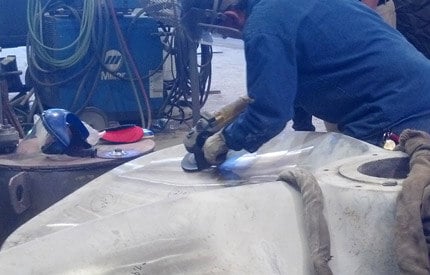
Schedule an On-site Assessment
The first step to cutting through barriers is to schedule a free on-site assessment where Weiler experts will evaluate how our abrasives can help eliminate inefficiencies, safety issues, and labor shortages in your operation.
Helping You Gain A Competitive Advantage
As an experienced global provider of abrasive solutions, Weiler Abrasives understands the unique needs of the shipbuilding and repair industry. We continuously innovate in response to emerging challenges to support the growth and sustainability of the shipbuilding and repair industry. Application experts work directly with shipbuilders at their facility to see production processes first-hand and work to resolve issues quickly. We help you choose the right abrasive for your applications to help you do more with less and increase efficiency, safety, and productivity.
Learn MorePrecision Cutting Wheels
Tiger Ceramic has been specifically designed for tough metal foundry applications, offering superior cuts and long life. These depressed center wheels can remove up to 40% more material than competitive zirconia products, resulting in more uptime and fewer abrasives replacements.
Weiler Abrasives has also incorporated an advanced anti-chipping technology to improve operator safety in the foundry operation. It eliminates uneven edge breakage and chipping and reduces the chance of flying debris during grinding. The technology also lengthens wheel life and offers a reliable grinding edge, while a triple fiberglass reinforcement design further increases wheel strength.
Weiler Abrasives also offers the Tiger Type 27 grinding wheel in zirconia and aluminum oxide grain — both performance tiers, with the ceramic setting the highest standard.
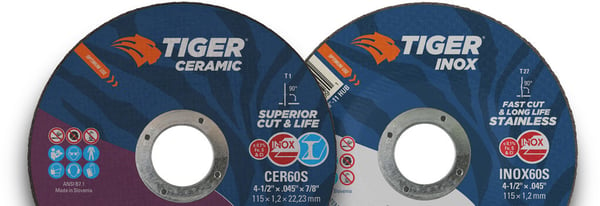
Grinding Wheels
When compared to competitive zirconia cups, Weiler Abrasives industry-exclusive ceramic grain technology allow the Tiger Ceramic cup grinding wheels to cut up to 30% faster. This results in high metal removal and improved productivity in the foundry cleaning room, especially on hard-to-grind materials. A balanced cup design reduces vibration and operator fatigue.
Each cup wheel includes a Weiler Abrasives exclusive safety feature — an anchored hexagon nut that secures the cup in place, locking it to the tool. Operators can have peace of mind when working on the most challenging metal casting foundry jobs, knowing that the cup is secure and resists breakage. This zinc-plated nut also resists oxidation and compared to cups with standard metal backs, offers up to three times higher torque holding strength and withstands double speed burst test ratings.
Tiger cup wheels are also available in zirconia for fast metal removal, silicon carbide for burnt sand castings and alumina oxide grains for cast iron metal foundry applications.
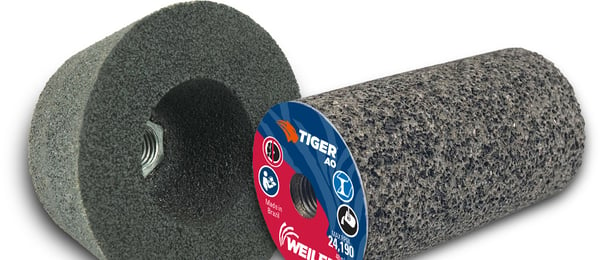
Flap Discs
For use with straight grinders, Tiger cones and plugs provide an aggressive cut-rate from start to finish. They are ideal for ID cleaning, hole edge beveling, cleaning castings in hard-to-reach areas. Each cone and plug feature an anchored, heavy-duty steel hex nut to secure the abrasives to the grinder and improve operator safety.
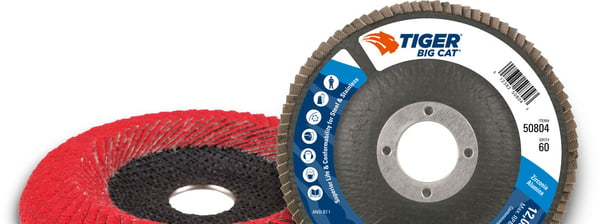
Power Brushes
Tiger Type 1 portable snagging wheels for pneumatic straight grinders and high frequency electric straight grinders support heavy stock removal, rough beveling, and snagging. They are available in 3, 6- and 8-inch wheels with double fiberglass reinforcements to increase strength and resist chipping.
Weiler Abrasives offers the cones, plugs and snagging wheels for the foundry cleaning room including Tiger Ceramic, Tiger Zirc and Tiger AO. Each abrasive type and grain provide smooth, vibration-free operation to improve operator comfort and lessen fatigue. An open face design also provides aggressive cut-rate right out of the box.
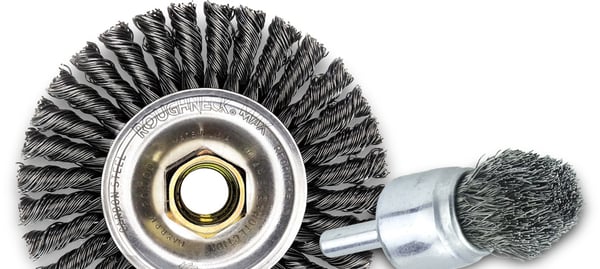
Resin Fiber Discs
Ideal for cleaning IDs, complex geometries, hard-to-reach places and more, Tiger Zirc mounted points are available in a variety of shapes. They feature an engineered stem bonding for strength, stability and safety and have a dressed work surface, so operators don’t need to break them in.
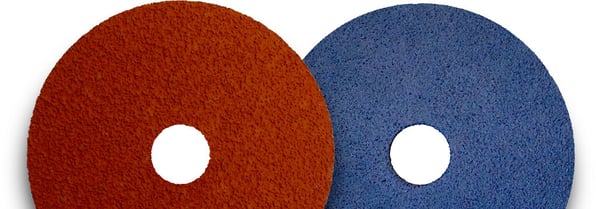
Find the abrasive products to boost your productivity
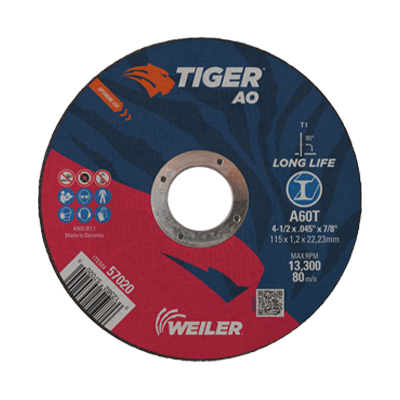
Precision Cutting Wheels Ensure Quick and Accurate Cuts
Cutting wheels, specifically designed for clean and precise cuts, are dependable for separating metal sections and swiftly and accurately cutting off unwanted material. Their exceptional durability and cutting performance increase efficiency, reducing production time and costs.
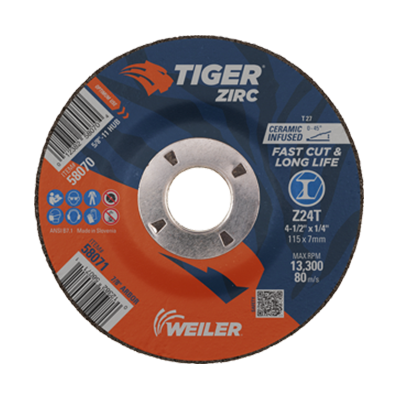
Optimized Shipyard Surface Preparation with High-Performance Grinding Wheels
Grinding wheels are indispensable for material removal, beveling and surface preparation. Choosing wheels in the correct size, style, abrasive grain, hardness, and grit size enable you to achieve the desired surface finish efficiently. By effectively preparing the surfaces, they enhance the adhesion of coatings, ultimately ensuring the longevity and durability of the ship's structure.
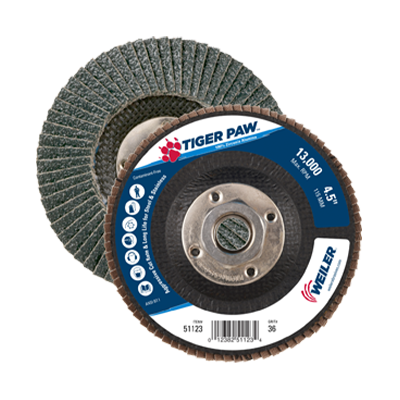
Impeccable Weld Seam Cleaning and Finishing with Flap Discs
Flap discs, consisting of overlapping abrasive flaps, are ideal tools for this task. They provide a controlled and uniform abrasive action, effectively removing weld spatter, excess material and smoothing rough edges. The versatility of flap discs allows users to achieve precise and consistent results, enhancing the welds' overall aesthetics and structural integrity.
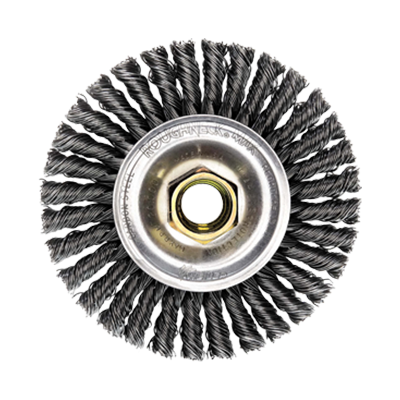
Enhancing Shipyard Efficiency with Power Brushes
Industrial wire brushes, inclusive of stringer brushes and end-brushes are essential for ship repair and maintenance, effectively eliminating rust and old coatings. In aluminum welding, stainless steel brushes are instrumental in preparing surfaces by removing oxides, ensuring robust welds for ship decks, and enhancing structural integrity. These brushes are built for long life and uphold the structural integrity of ships, particularly in demanding maritime environments.
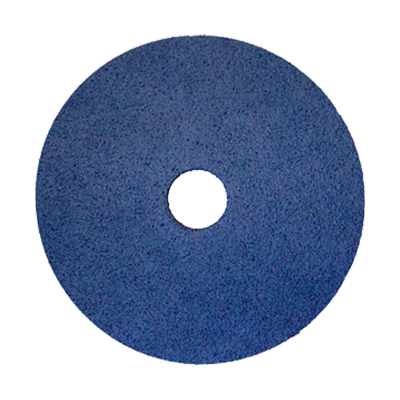
Fast and Effective Material Removal with Resin Fiber Discs
Resin fiber discs are effective for rapid material removal and surface preparation. These discs help remove oxidation, rust, old coatings, and surface irregularities before welding, painting, or adding new coatings to ship parts. This ensures full penetration and proper paint and coating adhesion.
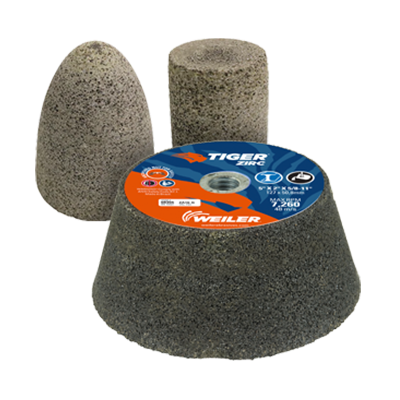
Work That Extra Mile with Additional Abrasives Solutions
In addition to Type 27 grinding wheels, which are the most common and work for a wide range of material removal applications, abrasive cones and plugs are used on tools like straight grinders and provide precision and control. These abrasives are ideal for in-hole beveling or grinding complex ship components, where space constraints may be an issue. Grinding cup wheels are abrasives used in shipbuilding and ship repair for grinding, shaping, and smoothing metal surfaces. They effectively remove excess material, imperfections, and are used for heavy material removal.