Metal Foundry Case Study Tiger Grinding Wheels Reduce Abrasive Spend Over 40% for Foundry
Challenge:
A Northwest Metal Foundry that manufactures rock crusher teeth from white iron chrome requires finishing work by grinding away seams, vent tubes, and excess material. White iron chrome is a very hard metal, rated 4 times harder than carbon steel on the Hardness Brinell (HB) scale.
With competitor wheels, 5 operators, grinding 8-hour shifts, 6 days a week, used 600 wheels per month. On average, 3 parts were completed per wheel.
Solution:
After testing several grinding wheels, the foundry converted to Weiler Tiger aluminum oxide 9" grinding wheels. By switching to Tiger grinding wheels, the foundry was able to finish 5 parts per wheel, saving approximately $1,100 per month. In addition, grinding time was reduced.
Result:
The metal foundry's consumable abrasives cost went from $2.18 per finished part to $1.15 per finished part, a 48% reduction.
End-User Comments:
"Tiger grinding wheels are aggressive and maintain their grinding edge throughout the life of the wheel."
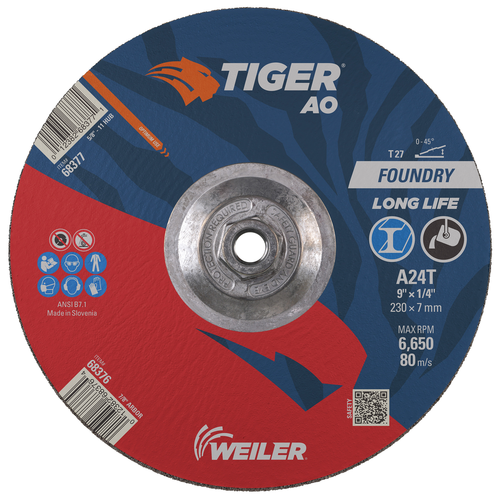
#68377 Weiler Tiger AO 9 x 1/4" Aluminum Oxide (AO) Grinding Wheel
40% More Work
$1,100/month
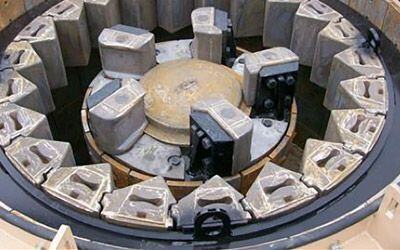
Finished shears in rock crusher.
Related Resources
Contact Us For Next Steps:
Call Weiler's Customer Experience Team at 800.835.9999. Our Application Engineers are available 8:30am to 5pm EST, Monday - Friday.
Or use our Application Assistance Form and one of our Engineers will recommend a process or the best product to solve your problem at the lowest possible end-use cost.